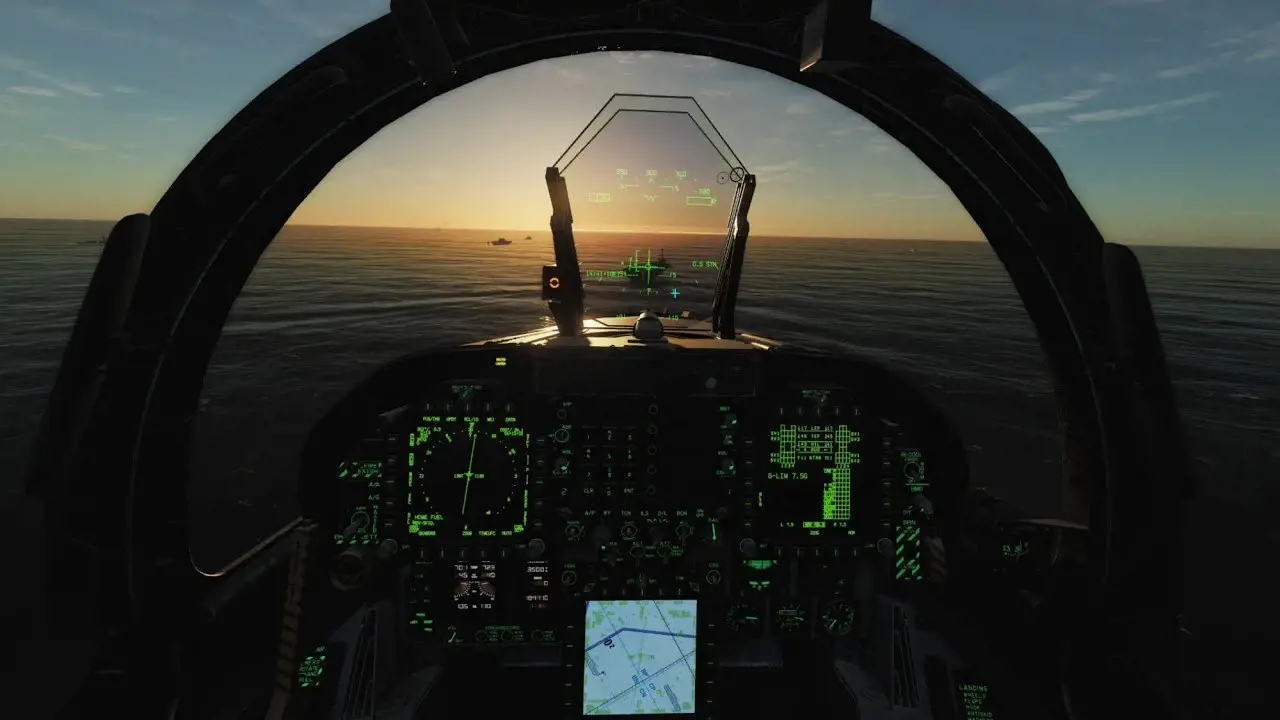
TEN TECH AEROSPACE & DEFENSE
Increasing Solver Stability and Productivity with Altair
About the Customer
TEN TECH AEROSPACE & DEFENSE, INC. (TEN TECH AERO) provides multi-disciplinary engineering services including high-end mechanical engineering design, analysis, physical testing support, hardware prototyping, and additive manufacturing services. Because their customer list includes, but is not limited to large defense contractors, accuracy and speed to result is a top priority. With decades of industrial experience and expertise in computer-aided engineering tools and methods, TEN TECH AERO can predict product performance without the use of costly physical prototypes during the design phase.
TEN TECH AERO prides themselves on being the most responsive, cost-effective, and highest quality partner in the market with repeat business average above 95% over the last decade. “Speed, quality and quantity do not have to be mutually exclusive,” says Managing Director, William Villers.
Their Challenge
With speed and accuracy as top priorities, TEN TECH AERO depends heavily on simulation tools that can consistently deliver with the highest performance possible. Several times a year, TEN TECH AERO conducts performance and stability re-evaluation of their tools to ensure they support the type of service that they are known for.
In 2022, their main finite element modeling production software, MSC APEX, saw a significant dip in performance and stability, resulting in severe data loss and inability to update legacy models to the latest release. This disrupted the company’s process, causing a loss of productivity and revenue.
Since the customer typically works with large models where more than 20 million degrees of freedom finite element models or 200 million grid thermal/CFD models are common, they knew they required a more robust solution to support all aspects of their computer-aided engineering (CAE) process, including preprocessing, solving and postprocessing. They also needed a tool that could work with their existing MSC Nastran legacy data, where thousands of models are generated over the course of a decade.
Solving time is a substantial issue for them as well. One of TEN TECH AERO’s competitive differentiators is that they do not charge their customers for solving and central processing unit (CPU) time. This means that additional time spent on solving, is time that is not spent on billable services. Shock and vibration analyses of complex models could take up to a day or more with MSC Nastran, and usually involved several additional tools to complete the analysis.
Figure 1: Navy Ship Turbine Fuel System DDAM Analysis
Our Solution
“I first heard about SimLab around two years ago, mainly because of their built-in BGA (Ball Grid Array) tools,” Villers says. “A significant part of our business for the last 3-4 years has been the support of Military System-in-a-Package (SiP) electronic component designs via simulation, from manufacturability studies to final shock and vibration and thermal performance prediction.”
Figure 2: System-in-a-Package Random Vibration Analysis
When TEN TECH AERO needed to explore a more efficient toolset than they currently had, they knew Altair® SimLab® would be strong contender. During their trial of Altair SimLab, TEN TECH AERO was able to not only recreate finite element models and perform complex analysis rapidly, but were also able to reuse and augment MSC Nastran legacy models, essentially transitioning away from their previous software with no data loss. In addition to built-in automation, they found that SimLab also had a visually appealing and very intuitive interface that allowed them to remain in the same tool for the entire process, from meshing and setup, to solving and visualization.
A few other things that really set Altair apart from other tools they were evaluating was their licensing model and the availability of training that is offered. The licensing model meant they weren’t tied to any one specific software; they would be able to take advantage of other tools within the Altair portfolio at no extra cost. “One of the things we enjoy is not having to use a specific product for our customers,”
Altair SimLab had an intuitive interface that allowed them to stay in the same tool for the entire process from meshing and setup to solving and visualization.